Introduction to Tank Fabrication Procedure
Tank fabrication is a crucial process in various industries, including oil and gas, chemical processing, and water storage. A well-executed fabrication procedure ensures durability, efficiency, and compliance with industry standards. In this guide, we will walk you through the fabrication procedure and highlight how Fabrimech excels in delivering high-quality tanks for diverse applications.
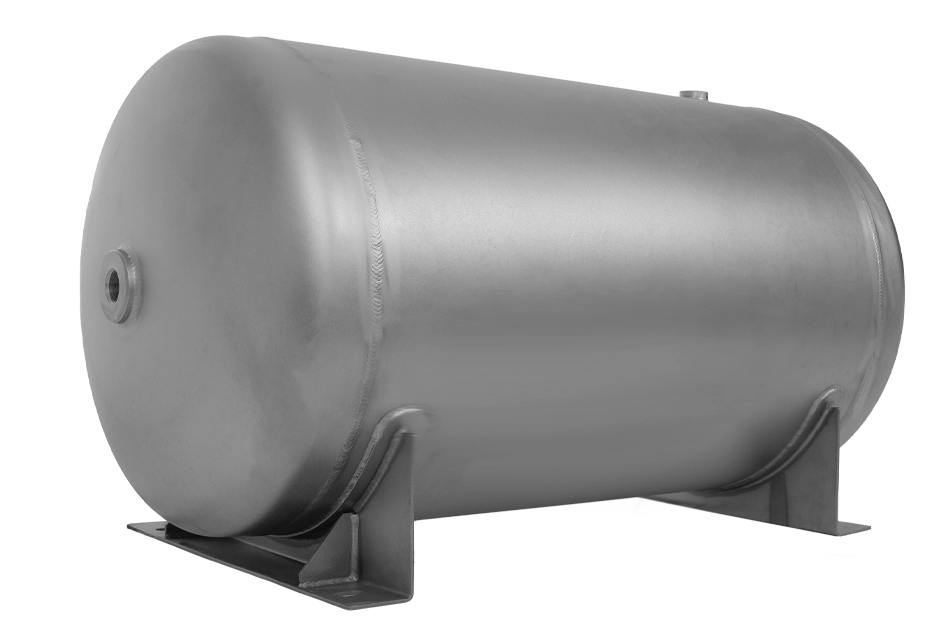
Step 1: Design and Material Selection
The fabrication procedure begins with an in-depth design process. Engineers at Fabrimech work closely with clients to determine the tank’s purpose, capacity, and material requirements. Manufacturers select materials like stainless steel, carbon steel, or aluminum depending on the application to ensure longevity and corrosion resistance.
Step 2: Cutting and Shaping
Once the design is finalized, the raw materials undergo cutting and shaping. Fabrimech utilizes advanced CNC cutting technology to achieve precision and minimize material waste. Plasma cutting, laser cutting, or waterjet cutting methods ensure that each component is fabricated with accuracy.
Step 3: Rolling and Forming
In this stage of the fabrication procedure, manufacturers roll and form metal plates into cylindrical or rectangular shapes, depending on the tank design. At Fabrimech, advanced rolling machines guarantee uniformity and precision; consequently, they ensure a perfect fit during assembly.
Step 4: Welding and Assembly
The fabrication team continues the procedure with welding, assembling and joining components using high-quality welding techniques. Skilled welders at Fabrimech employ MIG, TIG, or submerged arc welding, depending on the material and tank specifications. This step ensures structural integrity and leak-proof performance.
Step 5: Surface Treatment and Coating
To enhance durability, the tank surface undergoes treatment processes such as sandblasting, pickling, and passivation. Fabrimech applies protective coatings like epoxy, polyurethane, or rubber linings to prevent corrosion and ensure compliance with industry standards.
Step 6: Inspection and Quality Control
A critical part of the fabrication procedure is thorough inspection and quality control. Fabrimech follows stringent quality checks, including radiographic testing (RT), ultrasonic testing (UT), and hydrostatic pressure tests to ensure the tank meets all safety and regulatory requirements.
Step 7: Delivery and Installation
After passing all inspections, the finished tank is carefully transported to the client’s site. Fabrimech provides professional installation services, ensuring seamless integration with existing systems.
Have questions? We’re here to help!
Tank Fabrication Procedure by Fabrimech
At Fabrimech in Chennai, India, the tank fabrication procedure is a meticulously engineered process designed to deliver high-performance storage solutions for industrial applications. From material selection and design planning to welding, assembly, and final inspection, each stage is carried out under strict quality control to ensure durability, safety, and compliance with international standards.
Fabrimech specializes in the fabrication of tanks for oil, water, chemicals, and other industrial fluids, using advanced techniques such as MIG/TIG welding, CNC cutting, and non-destructive testing (NDT). The company’s experienced team ensures every storage tank meets specific client requirements while adhering to codes like ASME, API, and IS standards. With a commitment to innovation and precision, Fabrimech Chennai, India continues to set benchmarks in the tank fabrication industry.
Conclusion
A proper fabrication procedure is crucial for producing high-quality tanks that meet industry standards. Based in Chennai, India, Fabrimech combines expertise in precision engineering, advanced technology, and rigorous quality control to manufacture durable and reliable tanks. Whether you need storage tanks, pressure vessels, or custom-designed tanks, trust Fabrimech for efficient, compliant, and long-lasting fabrication solutions tailored to your specific needs.
For more details on tank fabrication or to get a quote, contact Fabrimech today!